Oracle Engineering
Oracle Engineering allows you to provide your design engineers with controlled access to item information, bills of material, and routings for items that are being designed. During the product lifecycle phases, Oracle Engineering allows you to record, track, and implement engineering changes to items, bills of material, and routings.
(The product life cycle goes through many phases, involves many professional disciplines, and requires many skills, tools and processes. Product life cycle (PLC) has to do with the life of a product in the market with respect to business/commercial costs and sales measures; whereas product lifecycle management (PLM) has more to do with managing descriptions and properties of a product through its development and useful life, mainly from a business/engineering point of view. To say that a product has a life cycle is to assert four things:
1) that products have a limited life,
2) product sales pass through distinct stages, each posing different challenges, opportunities, and problems to the seller,
3) profits rise and fall at different stages of product life cycle, and
4) products require different marketing, financial, manufacturing, purchasing, and human resource strategies in each life cycle stage.)
Developing Prototypes
While developing a product, most enterprises try to track the development in one engineering organization and then manufacture it in many plants. This concept of one engineering organization is not in the context of physical location. You may have designers/engineers who are located all over the world, but all of them belong to this virtual engineering community of a company.
You can define a single inventory organization in Oracle Applications to model your virtual engineering community and enable all the engineering items in this organization; when you’re ready to manufacture an item, you can transfer/copy that item to manufacturing and enable it in the appropriate manufacturing/distribution organizations.
Engineering Items
The difference between an engineering item and a manufacturing item is that they are controlled through different security functions. Typically, the ability to access (view and update) engineering items is given to a smaller group of users. Other than the ability to view and update the item information, engineering items behave exactly the same way as manufacturing items. For example, whether you can purchase an item or not is determined by the item attribute Purchaseable irrespective of that item being an engineering or a manufacturing item.
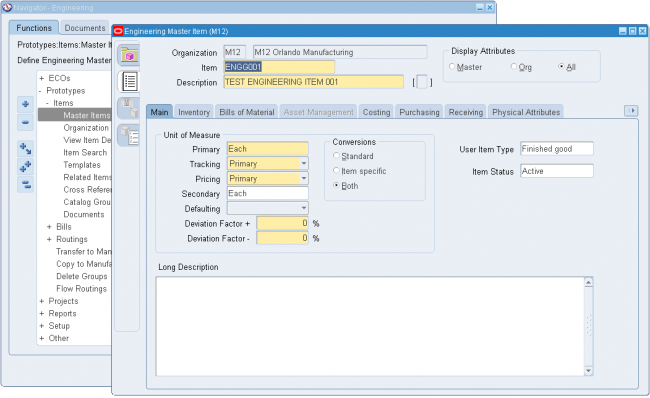
- You define engineering items in the Define Engineering Item form. In the real world, an item has many characteristics that could be identified by the item itself, or sometimes by the location in which it is stored. You can model these characteristics of an item using one of the two features—item attributes and item-subinventory attributes.
- For an engineering item, the item attribute Engineering Item is automatically checked(in Item Master BOM tab). You will not be able to update this attribute, although you can see it. You will not be able to view an engineering item using the Define Item form that is available through Oracle Inventory. You will be able to purchase, build, and sell an engineering item, based on the setting of its other item attributes.
- The Engineering Items: Revisions security function secures the ability to create revisions for an engineering item, whereas Engineering Items: Delete secures the ability to delete engineering items.
You can define the structure of your item as an engineering bill in the Engineering Bills of Material form. Because this is an “as designed” structure, it might not be used for manufacturing the product. So, you can define an Alternate called As Designed and use that to represent all your engineering structures.
You can define the operations to produce your item as an engineering routing in the Engineering Routing form. Similar to the component structure, you can use the As Designed label to distinguish your prototype routings.
Note
Unlike some ERP systems, Oracle Applications allow a particular item, bill of material, or routing to exist only in one environment (engineering or manufacturing) at a time; once you transfer the object from engineering to manufacturing, it no longer exists in engineering. To keep a separate copy of a bill or routing, you can create an alternate as described here. Alternatively, you can copy the engineering objects to manufacturing under a new item number; this alternative is discussed later in this chapter.
Accessing Engineering Information
The ability to access engineering items is controlled using function security. Any user who has the function Master Engineering Items in their menu has the ability to define/update engineering items. There is a corresponding function at the organization level called Organization Engineering Items, which controls the ability to edit engineering items in the enabled organizations.
Similarly, you can access engineering bills and routings if you have the functions Engineering Bills of Material and Engineering Routings in your responsibility.